Alumni Help Lead Eli Lilly Effort to Put COVID-19 Research on the Road
Monday, December 07, 2020
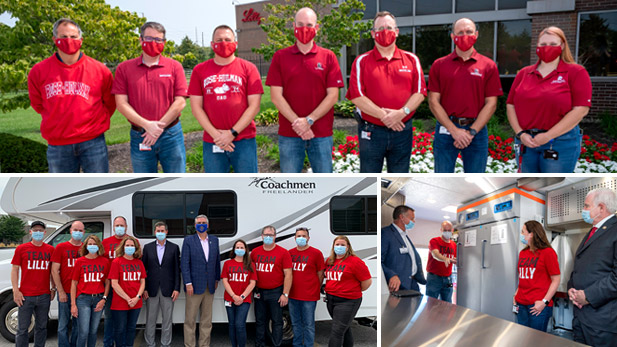
Alumni from a variety of engineering backgrounds, experience levels and positions came together to help Eli Lilly create a mobile research lab network that helped develop an antibody drug to prevent coronavirus spread in nursing homes.
In the first light of a mid-June morning, 1996 chemical engineering alumnus Brian Miesse scouted throughout a suburban Indianapolis dealership in search of just the right recreational vehicle for a once-in-a-lifetime cross country journey.
And, he wasn’t planning an exotic summer vacation.
Rather, the RV would be customized to create a mobile research lab network to study the effectiveness of an Eli Lilly and Company antibody drug to prevent coronavirus spread in America’s nursing homes. The effort to enlist up to 2,400 people for a trial of Lilly’s LY-CoV555 investigational product is being conducted in partnership with the National Institute of Allergy and Infectious Diseases, the COVID-19 Prevention Network, and several long-term care facility networks across the country.
Nursing home residents and staff members account for more than 40% of COVID-19 deaths in the U.S., according to federal agency statistics.
Abiding by the company’s “the patient is waiting” mantra, Lilly officials knew that it was critical to include the elderly population in its research studies. However, clinical trials usually take place in hospitals, universities, doctors’ offices, and community clinics, not long-term care facilities. And, pandemic-mandated facility lockdowns, patient mobility limitations, and staff shortages provided further complications.
Every day also added cases and deaths to the health care crisis.
So, Miesse and his team proposed the idea of converting RVs to become mobile research units (MRUs)—similar to mobile medic clinics, modular clinics, and bloodmobiles. The next morning, he had found a Coachman RV model at the local dealership to meet the project’s specifications. Late that same evening the idea was approved by Lilly’s leadership, which saw the need to be able to test the company’s drug in nursing homes within days after an infection was identified.
“COVID-19 has had a devastating impact on nursing home residents. We’re working as fast as we can to create medicines that might stop the spread of the virus to these vulnerable individuals. While it’s not easy to conduct clinical trials in this setting, we’re taking on the challenge in an effort to help those who need us the most,” said Daniel Skovronsky, M.D., Ph.D., Lilly’s chief scientific officer and president of Lilly Research Laboratories, in a Lilly press release.
With top-level corporate support, it didn’t take long for other Rose-Hulman alumni within Lilly’s clinical development, clinical supply, and engineering teams to help colleagues in brainstorming.
Indiana-based Coachmen called dealerships across the country and got the vehicles delivered to Indianapolis within days. Traditional interior amenities were removed in order to retrofit customized storage solutions for equipment, laboratory space, and clinical trial material preparation. Room also had to be found for custom controlled-temperature storage, system monitoring equipment, and a lengthy list of technology.
Incredibly, it took only 30 days to create the first of the original eight MRUs and late-stage trials had started by August. The labs became so critical to the study that several more were added to the fleet.
“This project involved herculean efforts by everyone on the project team to deliver in the shortest time possible,” cited 1986 chemical engineering alumnus Kirk Caraway, global quality auditor for Lilly’s commercial pharmaceutical projects. He points out that all engineering projects are dictated by three resources: People, time, and money. All three areas were aligned to make this project “like none other,” Caraway concedes, adding, “Never before have I felt closer to the patient, closer to having such an immediate and direct impact on a global need as I have on this project. If we can save the life of one person, make just one person’s life better with this antibody therapy, all the thousands of hours expended by so many at Lilly will be worth it.”
The engineering team’s biggest technical challenge was ensuring the clinical trial materials and supplies were always stored at the proper temperatures and had the data to prove it. They solved this by incorporating four energy sources (electric plug-in at each nursing home, a battery pack, and two onboard electric generators) to feed all of the distinctly different equipment inside each unit—maintaining the research project’s integrity.
“Fortunately, as Lilly engineers, we recognize the importance of the science involved within a project, and the scientists value engineering’s role in making things possible. This project was a perfect marriage of technology and science,” says Miesse, a 22-year Lilly employee.
And, the project struck an emotional chord with Miesse, whose father-in-law had tested positive with the coronavirus as a nursing home resident.
“Everything about this project was big, including the high stakes for everyone involved. We had to keep our eyes on the prize: contributing to people’s health and wellness,” he states. “Early on, the project parameters were changing hourly and there were 16-hour workdays for a couple of months. It took us two and a half weeks to design and build the first RV, and by the end, we had the process down to five to six days.”
The contributions of 2001 electrical engineering alumna Amanda (Rice) Plance, an associate senior consultant engineer, came from Ireland, where she had just taken a short-term company global work assignment.
“This project really goes to show you that with the right team, and everyone trying to achieve a common goal, the sky’s the limit,” she remarks. “We had a lot of little bumps in the road, but we were able to overcome them with amazing teamwork and dedication.”
The project team also included significant technical contributions from a small group of Indiana-based contract companies. Cornerstone Controls lead engineer Leonard Clark, a 1997 chemical engineering graduate, says, “I’ve really enjoyed how relatable this project has been. Normally, I can talk with my family about processes and equipment that might sound vaguely familiar, but generally don’t mean anything specific to them. We’ve all seen an RV on the road. And, we have all experienced the effects of COVID-19 on our lives. So, it’s been gratifying to make that connection and have others appreciate the potential for our work.”
-----------
Lots of Moving Project Parts
The roles and responsibilities of alumni and parents associated with Eli Lilly & Company’s mobile medicine project were:
Brian Miesse (CHE, 1996), associate senior consultant engineer in Lilly’s Global Facilities Delivery, proposed the original concept of the converted RVs to Eli Lilly and Company’s leadership team and eventually led the engineering team that oversaw the retrofit and qualification activities.
Rick Kocken (EE, 1990), associate senior consultant engineer at Lilly’s Engineering Tech Center, designed the electrical system that had the capacity to feed all electrical loads, reliability through redundant and alternative power sources, and ease of operation by all staff.
Kirk Caraway (CHE, 1986), global quality auditor for Lilly’s commercial pharmaceutical projects, brought more than 34 years of design, construction, manufacturing, and quality experience to the project. He quickly identified and help correct design issues, and had final approval for all pharmaceutical activities affecting product and patient safety.
Amanda (Rice) Plance (EE, 2001), associate senior consultant engineer with Lilly, led the design of the temperature monitoring and alarming system for each unit’s refrigerators and freezers.
Leonard Clark (CHE, 1997), lead engineer with contractor Cornerstone Controls, addressed unique challenges with data integration and visualization.
Ellie Honious (ME, 2018), staff engineer with contractor Performance Validation, helped integrate the complex technical support system, keeping such items as temperature data loggers, wireless access points, refrigerators, and freezers providing 24-hour data collection.
D.R. Foley (CHE, 1988), senior director of global facilities delivery, provided administrative support and encouragement.
Jason Duff (CHE, 1989), director of profiling and design for global facilities delivery, assisted in removing internal obstacles that kept the project on its timeline and the team motivated to meet its goals.
Kevin Baker (Rose Parent), associate consultant engineer with Lilly, oversaw the installation and qualification of the temperature monitoring equipment and data historian configuration.
And, he wasn’t planning an exotic summer vacation.
Rather, the RV would be customized to create a mobile research lab network to study the effectiveness of an Eli Lilly and Company antibody drug to prevent coronavirus spread in America’s nursing homes. The effort to enlist up to 2,400 people for a trial of Lilly’s LY-CoV555 investigational product is being conducted in partnership with the National Institute of Allergy and Infectious Diseases, the COVID-19 Prevention Network, and several long-term care facility networks across the country.
Nursing home residents and staff members account for more than 40% of COVID-19 deaths in the U.S., according to federal agency statistics.
Abiding by the company’s “the patient is waiting” mantra, Lilly officials knew that it was critical to include the elderly population in its research studies. However, clinical trials usually take place in hospitals, universities, doctors’ offices, and community clinics, not long-term care facilities. And, pandemic-mandated facility lockdowns, patient mobility limitations, and staff shortages provided further complications.
Every day also added cases and deaths to the health care crisis.
So, Miesse and his team proposed the idea of converting RVs to become mobile research units (MRUs)—similar to mobile medic clinics, modular clinics, and bloodmobiles. The next morning, he had found a Coachman RV model at the local dealership to meet the project’s specifications. Late that same evening the idea was approved by Lilly’s leadership, which saw the need to be able to test the company’s drug in nursing homes within days after an infection was identified.
“COVID-19 has had a devastating impact on nursing home residents. We’re working as fast as we can to create medicines that might stop the spread of the virus to these vulnerable individuals. While it’s not easy to conduct clinical trials in this setting, we’re taking on the challenge in an effort to help those who need us the most,” said Daniel Skovronsky, M.D., Ph.D., Lilly’s chief scientific officer and president of Lilly Research Laboratories, in a Lilly press release.
With top-level corporate support, it didn’t take long for other Rose-Hulman alumni within Lilly’s clinical development, clinical supply, and engineering teams to help colleagues in brainstorming.
Indiana-based Coachmen called dealerships across the country and got the vehicles delivered to Indianapolis within days. Traditional interior amenities were removed in order to retrofit customized storage solutions for equipment, laboratory space, and clinical trial material preparation. Room also had to be found for custom controlled-temperature storage, system monitoring equipment, and a lengthy list of technology.
Incredibly, it took only 30 days to create the first of the original eight MRUs and late-stage trials had started by August. The labs became so critical to the study that several more were added to the fleet.
“This project involved herculean efforts by everyone on the project team to deliver in the shortest time possible,” cited 1986 chemical engineering alumnus Kirk Caraway, global quality auditor for Lilly’s commercial pharmaceutical projects. He points out that all engineering projects are dictated by three resources: People, time, and money. All three areas were aligned to make this project “like none other,” Caraway concedes, adding, “Never before have I felt closer to the patient, closer to having such an immediate and direct impact on a global need as I have on this project. If we can save the life of one person, make just one person’s life better with this antibody therapy, all the thousands of hours expended by so many at Lilly will be worth it.”
The engineering team’s biggest technical challenge was ensuring the clinical trial materials and supplies were always stored at the proper temperatures and had the data to prove it. They solved this by incorporating four energy sources (electric plug-in at each nursing home, a battery pack, and two onboard electric generators) to feed all of the distinctly different equipment inside each unit—maintaining the research project’s integrity.
“Fortunately, as Lilly engineers, we recognize the importance of the science involved within a project, and the scientists value engineering’s role in making things possible. This project was a perfect marriage of technology and science,” says Miesse, a 22-year Lilly employee.
And, the project struck an emotional chord with Miesse, whose father-in-law had tested positive with the coronavirus as a nursing home resident.
“Everything about this project was big, including the high stakes for everyone involved. We had to keep our eyes on the prize: contributing to people’s health and wellness,” he states. “Early on, the project parameters were changing hourly and there were 16-hour workdays for a couple of months. It took us two and a half weeks to design and build the first RV, and by the end, we had the process down to five to six days.”
The contributions of 2001 electrical engineering alumna Amanda (Rice) Plance, an associate senior consultant engineer, came from Ireland, where she had just taken a short-term company global work assignment.
“This project really goes to show you that with the right team, and everyone trying to achieve a common goal, the sky’s the limit,” she remarks. “We had a lot of little bumps in the road, but we were able to overcome them with amazing teamwork and dedication.”
The project team also included significant technical contributions from a small group of Indiana-based contract companies. Cornerstone Controls lead engineer Leonard Clark, a 1997 chemical engineering graduate, says, “I’ve really enjoyed how relatable this project has been. Normally, I can talk with my family about processes and equipment that might sound vaguely familiar, but generally don’t mean anything specific to them. We’ve all seen an RV on the road. And, we have all experienced the effects of COVID-19 on our lives. So, it’s been gratifying to make that connection and have others appreciate the potential for our work.”
-----------
Lots of Moving Project Parts
The roles and responsibilities of alumni and parents associated with Eli Lilly & Company’s mobile medicine project were:
Brian Miesse (CHE, 1996), associate senior consultant engineer in Lilly’s Global Facilities Delivery, proposed the original concept of the converted RVs to Eli Lilly and Company’s leadership team and eventually led the engineering team that oversaw the retrofit and qualification activities.
Rick Kocken (EE, 1990), associate senior consultant engineer at Lilly’s Engineering Tech Center, designed the electrical system that had the capacity to feed all electrical loads, reliability through redundant and alternative power sources, and ease of operation by all staff.
Kirk Caraway (CHE, 1986), global quality auditor for Lilly’s commercial pharmaceutical projects, brought more than 34 years of design, construction, manufacturing, and quality experience to the project. He quickly identified and help correct design issues, and had final approval for all pharmaceutical activities affecting product and patient safety.
Amanda (Rice) Plance (EE, 2001), associate senior consultant engineer with Lilly, led the design of the temperature monitoring and alarming system for each unit’s refrigerators and freezers.
Leonard Clark (CHE, 1997), lead engineer with contractor Cornerstone Controls, addressed unique challenges with data integration and visualization.
Ellie Honious (ME, 2018), staff engineer with contractor Performance Validation, helped integrate the complex technical support system, keeping such items as temperature data loggers, wireless access points, refrigerators, and freezers providing 24-hour data collection.
D.R. Foley (CHE, 1988), senior director of global facilities delivery, provided administrative support and encouragement.
Jason Duff (CHE, 1989), director of profiling and design for global facilities delivery, assisted in removing internal obstacles that kept the project on its timeline and the team motivated to meet its goals.
Kevin Baker (Rose Parent), associate consultant engineer with Lilly, oversaw the installation and qualification of the temperature monitoring equipment and data historian configuration.