Design-Build-Fly: “You have to do the math”
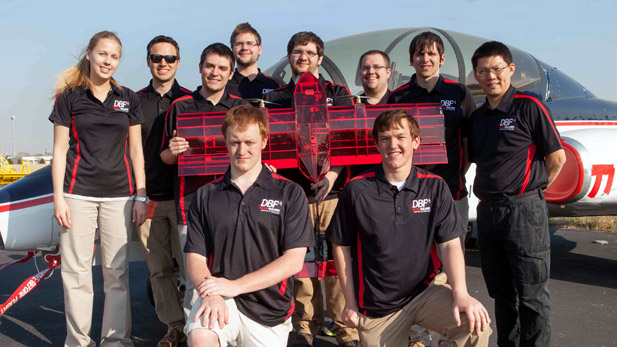
The Rose-Hulman Design-Build-Fly team traveled to Wichita, Kansas, April 19-22 for the annual flyoff sponsored by the American Institute of Aeronautics and Astronautics. Student teams from 109 colleges worldwide competed.
Don’t you hate it when your plane crashes in high winds, damaging a wing and detaching the landing gear?
Some of us would never fly again. The Rose-Hulman Design-Build-Fly team opted to build virtually a new craft from spare parts and get back into the competition.
Gusts reached 30-40 mph in Wichita, Kansas, April 19-22 for the annual flyoff sponsored by the American Institute of Aeronautics and Astronautics. Student teams from 109 colleges worldwide competed.
Each team was required to design and construct an unmanned, electric-powered, radio-controlled aircraft to meet rigorous specifications, then demonstrate its capabilities in simulated commercial missions. Each year of the competition, teams confront new tasks: for 2018, each craft had to fly empty, then with simulated passengers (Super Balls), and again with simulated cargo added (blocks).
Day One was windy, and the RHIT plane—super-light for efficiency and flying without passengers or cargo—was damaged in a crash. Team members (13 Mechanical Engineering majors, including five seniors and eight underclassmen) had to rebuild the craft from spare parts.
The original plane had performed well in on-campus testing, says Matt Riley, assistant professor of mechanical engineering. Weather conditions deteriorated the second day (rain and 40-mph winds), but the rebuilt Rose-Hulman plane performed well carrying a load on Day Three.
Not for hobbyists
Design-Build-Fly is as far from backyard drone-driving as Formula One is from parking lot tire-squealing.
In addition to in-flight tests with and without simulated passengers and cargo, teams are rated on reports detailing their conceptual designs, budgeting and testing protocols. The Rose-Hulman team did well on that score, coming in 32nd of the 101 teams.
An added challenge, says Riley, was the timed replacement of two randomly selected components, using only parts and tools contained in the aircraft’s cargo hold. The team caught a break when the die roll called for a battery swap—easier to accomplish than some components. Together with replacement of a wing aileron, the RHIT team pulled off the task in just five of the allotted eight minutes.
The DBF experience taught the team to make decisions based on evidence and not just hunches, says Riley. “You have to brainstorm and come up with off-the-wall ideas, but you also have to do the math.”