Learning to Program Robots for a Human-Friendly Workplace
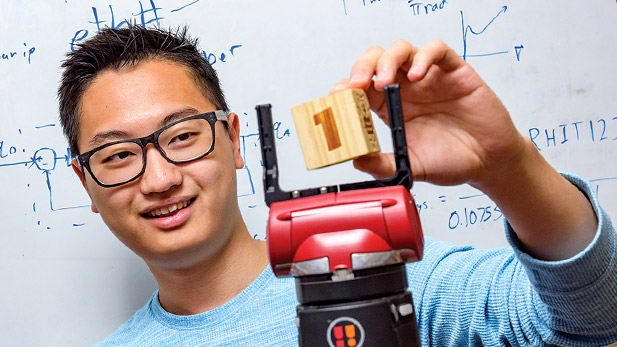
Students taking Dr. Winck's Robot Dynamics and Control class learn how to model the kinematics and dynamics of industrial robot arms and how to control them.
Students taking Robot Dynamics and Control (ME497) quickly find that the course is theoretical, but with clear practical applications. Students learn how to model the kinematics and dynamics of industrial robot arms and how to control them. Dr. Ryder Winck, assistant professor of mechanical engineering, says, “One of the best aspects of this class is the clear connection between the material and its application. Most of the assignments involve modeling actual industrial robot arms.” ME497 is required for the Robotics minor, but open to all Rose-Hulman. Most in the class are juniors and seniors.
Students are exposed to some more advanced control techniques. Early industrial robots, says Winck, were used mainly for tasks such as welding, with limited movements (perhaps back and forth in an assembly line). Their momentum could be lethal to human co-workers. Impedance or force control required expensive sensors which were impractical in a factory setting.
Now, says Winck, robots are increasingly designed to work well around people. Some, such as Rose-Hulman’s Sawyer Robot, move more slowly and have built-in, low-cost joint-torque sensors. Sawyer’s arm can be programmed with force control, giving it a softer, more nuanced touch. Winck uses writing as an analogy: “You need to control the force of the tip of the pen, and move the position of the tip. The challenge is to control force in a particular direction, and control movement in other directions.”
Students who master ME497 material have opportunities for independent study projects like the team that worked on the AI X-prize in 2016.